
UNDERSTANDING SIPOC FRAMEWORK FOR BUSINESS EVALUATION (Blog 1 of 4)
by Jon Colen
10/19/2023
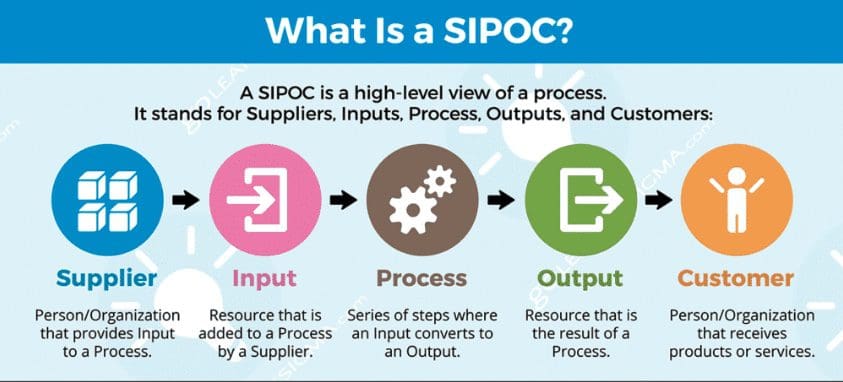
In most businesses, > 90% of resources are spent performing non-value added activities. Thus, the biggest evaluation benefits are driven by eliminating waste or at least understanding what drives it.
When it comes to evaluating and improving your business processes, the SIPOC framework is a valuable tool. SIPOC, which stands for Suppliers, Inputs, Process, Outputs, and Customers, is a process mapping and analysis tool that provides a comprehensive view of your business processes. In essence, SIPOC is the Process that is your business. Each process involves a set of activities or tasks, which may be performed by individuals, machinery, or computer systems with a specific purpose in mind.
In this blog, we’ll introduce you to the SIPOC framework, explaining each component and how it can help you gain a better understanding of your business operations. We’ll also discuss its benefits and why it’s a fundamental tool for business process improvement.
SUPPLIERS
Whoever provides the Input (material or information) of a Process. The concept of a supplier in Lean Six Sigma extends beyond traditional suppliers of physical goods and encompasses any factor that contributes to or influences a process.
INPUTS
The material or data which “Enters” and is “Used” or “Changed” in or by the Process.
PROCESS
A group or series of logically related activities and tasks involving People, Procedures, Machines, Computers & Documents needed to Change materials and/or information into a specified Product, Service or Information Output.
OUTPUTS
Consists of Material, Service, Data or Documents resulting from the Operation or Process Step
CUSTOMERS
There are two types, Internal and External. For purposes of your business, whomever Receives the Output of a Process is a Customer.
BENEFITS
Now that you have some understanding of the roles within this framework, let’s review some of the benefits:
- Clarity and Understanding: SIPOC provides a visual representation of a process, making it easier for stakeholders to understand how the process functions and the flow of inputs and outputs.
- Scope Definition: SIPOC helps in clearly defining the boundaries of a process. It identifies the suppliers, inputs, and customers involved, ensuring that everyone has a shared understanding of the process’s scope.
- Identification of Key Elements: It highlights the key components of a process, this identification is essential for process analysis and improvement.
- Focus on Customer Requirements: SIPOC encourages a customer-centric perspective by emphasizing the needs and requirements of the end customers. This can lead to improved customer satisfaction and product/service quality.
- Process Optimization: By visualizing the process, SIPOC makes it easier to identify bottlenecks, redundancies, and areas for improvement. This, in turn, facilitates process optimization and efficiency enhancements.
- Cross-Functional Understanding: SIPOC is particularly useful in cross-functional teams, as it helps individuals from different departments or roles to understand how their work fits into the larger process.
- Change Management: When changes are introduced to a process, SIPOC can be used to assess how these changes impact the overall workflow, suppliers, inputs, outputs, and customers. It aids in managing change effectively.
- Risk Identification: SIPOC can reveal potential risks or areas of vulnerability in a process by highlighting dependencies and interfaces with suppliers and customers.
- Communication: SIPOC serves as a communication tool, helping teams and stakeholders discuss and document the process in a structured and systematic manner.
- Baseline for Metrics: It provides a baseline for measuring process performance and improvement over time. Metrics can be associated with specific inputs, outputs, and process steps identified in the SIPOC.
- Quality Assurance: SIPOC aids in ensuring that process steps align with quality standards and customer expectations, promoting consistency and reducing errors.
THE WRAP-UP
In summary, using a SIPOC diagram offers a structured and visual approach to understanding, analyzing, and improving processes. Its benefits include increased clarity, scope definition, cross-functional understanding, process optimization, and a customer-centric perspective, among others. These advantages make SIPOC a valuable tool in process management, quality improvement, and process change initiatives.
Need help with your business? Email us sales@asktconsulting.com for a personalized consultation.