
UNDERSTANDING SIPOC FRAMEWORK FOR BUSINESS EVALUATION (Blog 2 of 4)
by Jon Colen
10/24/2023
CREATING A SIPOC DIAGRAM
In this blog, we’ll guide you through the process of constructing a SIPOC diagram step by step. We’ll explain how to identify your process, its suppliers, inputs, outputs, and customers. We’ll also provide examples to illustrate how the SIPOC framework can be applied to different types of businesses. By the end of this blog, you’ll have a clear understanding of how to create a SIPOC diagram to assess your business operations.
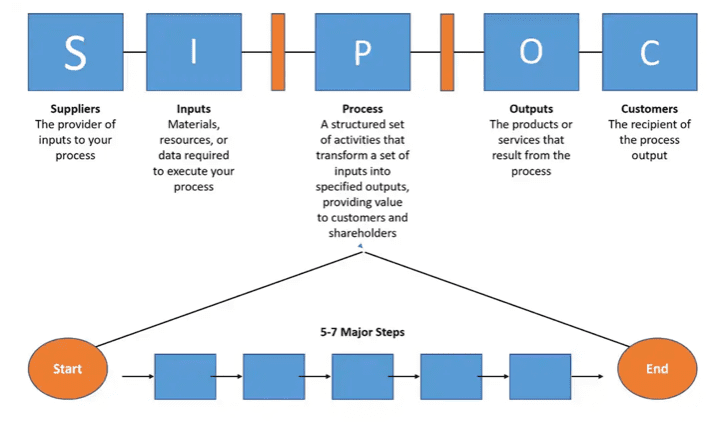
Creating a SIPOC (Suppliers, Inputs, Process, Outputs, and Customers) diagram is a structured way to understand and document a process, especially in the context of process improvement or analysis.
WHAT IS A SIPOC DIAGRAM USED FOR?
A SIPOC diagram is a type of workflow diagram or process map that improves business processes by clearly defining how your system or process works. They can be used to identify areas of inefficiency, areas for improvement, and potential risks.
Before we begin, please review a sample legend for a process map:
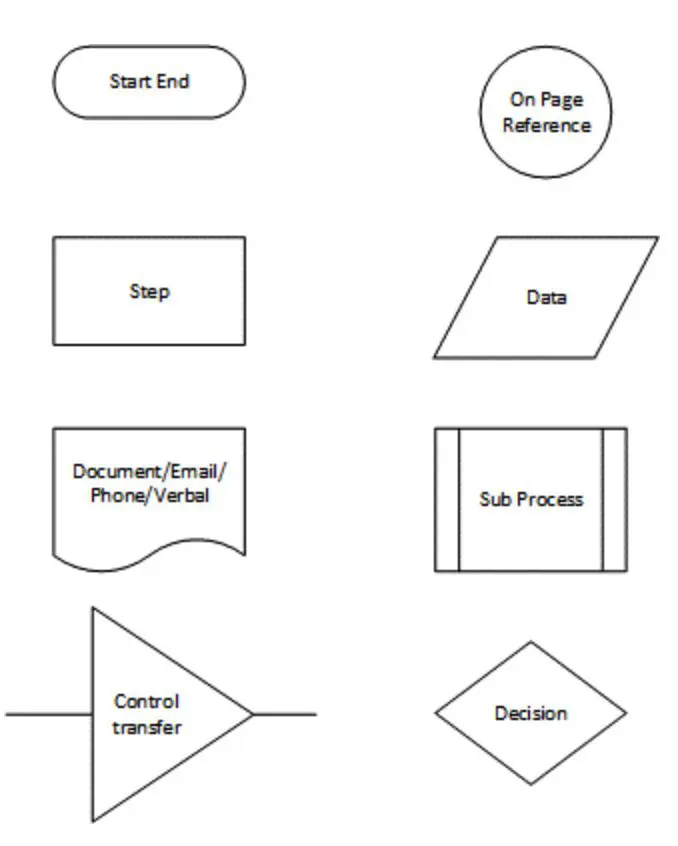
HERE ARE THE STEPS TO CREATE A SIPOC DIAGRAM:
Define the Purpose:
Begin by clearly defining the purpose and scope of the process you want to document. What is the specific process you want to analyze or improve? Make sure you have a clear objective in mind.
Identify the Process Boundaries:
Determine the starting and ending points of the process. What are the key inputs and outputs? This helps in defining the scope of your SIPOC diagram.
Identify the Elements:
List the five key elements of a SIPOC – Suppliers, Inputs, Process, Outputs, and Customers. These are the categories you’ll fill in as you document the process.
Identify Suppliers:
Suppliers are the entities or individuals who provide inputs to the process. List all the suppliers relevant to your process. This might include external vendors, other departments, or internal sources.
Identify Inputs:
Inputs are the materials, information, or resources provided by the suppliers. List all the inputs that are essential to the process. Be specific and thorough in identifying them.
Identify the Process Steps:
Describe the steps or activities that make up the process. You can use a flowchart or a simple list to outline these steps. This is the “P” (Process) section of the SIPOC.
Identify Outputs:
Outputs are the results or deliverables produced by the process. List all the outputs that result from the process steps. Be specific about what is produced.
Identify Customers:
Customers are the entities or individuals who receive the outputs of the process. List all the customers who are affected by the outputs. This might include internal teams, external clients, or other stakeholders.
Connect the Elements:
Draw arrows or lines to connect the elements in your SIPOC diagram. Connect the suppliers to the inputs, the inputs to the process steps, the process steps to the outputs, and the outputs to the customers. This visual representation helps to illustrate the flow of the process.
How to Process a Customer Order for PB&J
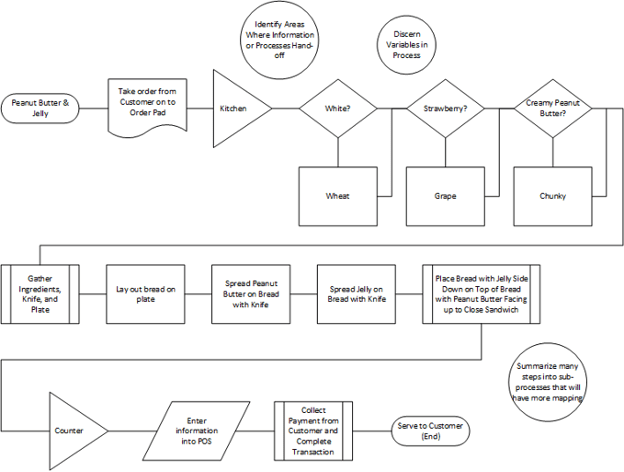
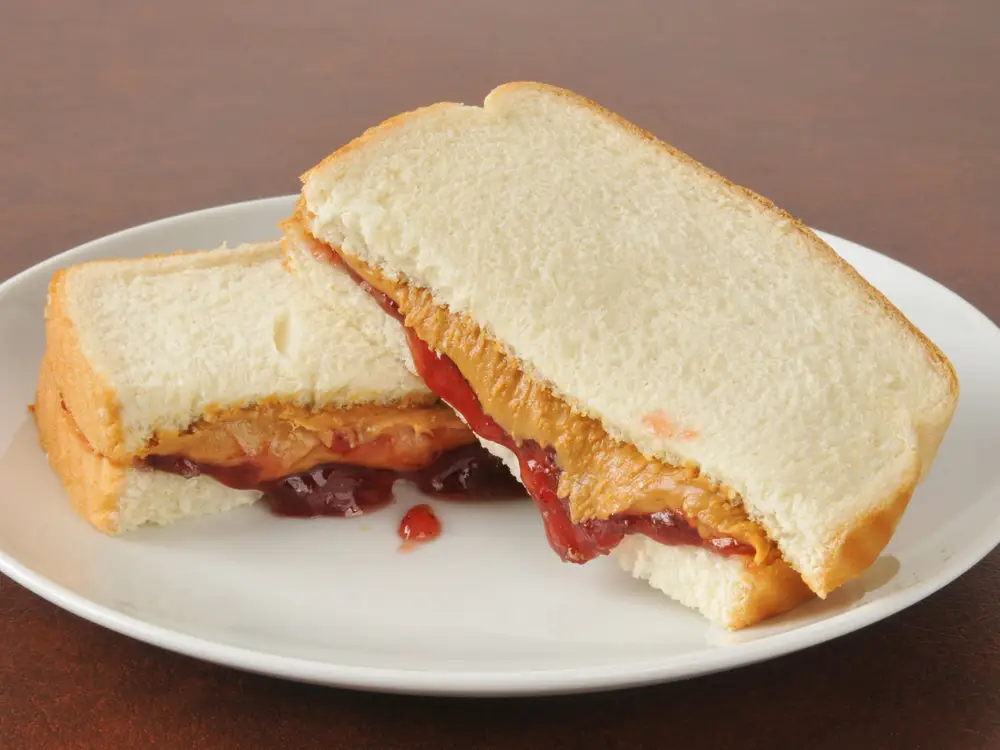
Gather Additional Information:
While creating the SIPOC diagram, collect relevant data or details about each element. This might include specifications, quantities, timelines, or any other pertinent information.
Review and Validate:
Review the SIPOC diagram with stakeholders and subject matter experts to ensure accuracy and completeness. Make any necessary revisions based on their feedback.
Use and Analyze:
Once your SIPOC diagram is complete, use it as a reference for process analysis, improvement, or communication. It provides a clear overview of the process, making it easier to identify areas for enhancement and to communicate the process to others.
THE WRAP-UP
SIPOC diagrams are valuable tools for process understanding, documentation, and improvement. They provide a high-level view of how a process works and how it interacts with suppliers and customers. This visual representation can aid in process optimization and enhance overall process management.